SIGMA CEOインタビュー(その1)
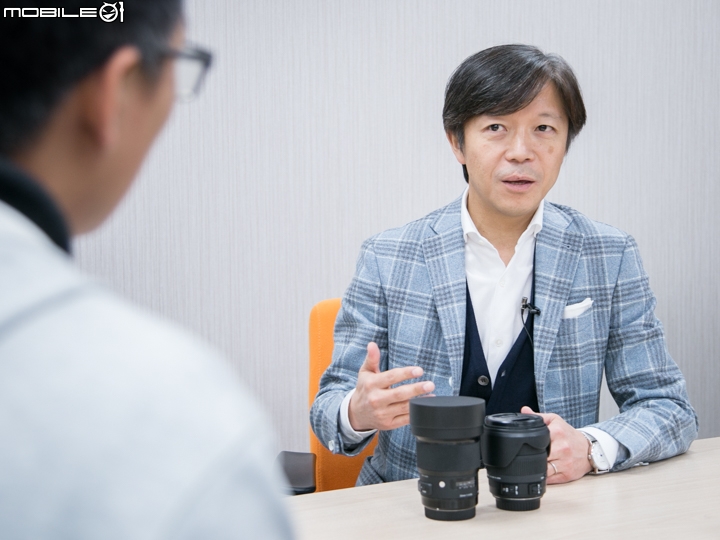
Q:まず、一番大きな疑問なのですが、なぜ台湾に来てメディアや地元の販売店と話をしようとしているのですか?カメラ会社のCEOが行うことではないと思うのですが。
A:初めて台湾に来たのは3年前になります。創業者である私の父が他界しまして、私が会社を引き継ぐことになりました。その時、私は海外のマーケットを直接見て回りたいと思ったのです。台湾に来た理由の一つは、私の母が台北で生まれたからですね。母は日本人なのですが、第二次大戦の前に商売上の理由で一家が台湾に移って来たのです。母はいつも台湾の良い所について私に話してくれました。それでここに来たいと思うようになったのです。
Q:2ヶ月ほど前に「湾生回家」というドキュメンタリーが放送されました。あなたの母のような台湾生まれの日本人を「湾生」と呼ぶのですが、その人達の話です。第二次大戦後にそういった人たちは日本に帰ってしまったのですが、彼らは本当にかつての台湾での生活を懐かしがっているのですね。このドキュメンタリーはぜひ見て欲しいと思います。ほとんどの場面は日本語で話されていますから、これを見ればあなたの母が台湾についてどのような感情を抱いているか、わかると思います。
製品のデザインについて
Q:さて、製品についての話に移りましょう。シグマの製品のデザインは大きく変わってきていると思うのですが、その理由は何ですか?
A:CEOになったあとで、商品ラインナップの再編に取り組みました。それ以前は様々な部署の管理者をしていました。光学部、ソフトウェア部、知的財産権部、その他にもいくつかのプロジェクトの責任者もしました。その時にわかったのが、製品のコンセプトを消費者にうまく伝えられないことがある、ということです。例えば、高品質なレンズを作るとすると、大きく重たくなります。消費者がその製品の背後にあるコンセプトを理解していないと、その製品を良いものだと思わなくなるかもしれません。
なので、まずは製品のコンセプトをはっきりさせようと考えました。そして、消費者がコンセプトをわかりやすくなるように、製品ラインナップを分けることにしたのです。また、私が個人的に工業デザインが好きだということもあります。カメラとか、車、オーディオなどの一般的な工業デザインですね。私が10代だった70年代から80年代には、デザイン的に優れた製品がいくつか売られていたんです。
Q:ご自身が好きな製品をいくつか教えてくれますか?
A:ソニーの80年代の製品デザインは素晴らしいですね。90年代のバング・アンド・オルフセン。これは私が生まれる前ですけど、60年代のブラウンのデザイン。ブラウンはラジオやオーディオをたくさん作っていました。私はそういうものが好きなので、自社の製品もシンプルで洗練されたものにしていきたいですね。
ただ、レンズの設計に関しては話は別です。レンズで最も重要なのは性能です。鏡筒のデザインではありません。何か装飾的なものをレンズに付け加えたら、おそらくやり過ぎになってしまうでしょう。したがって、レンズについては「デザインしないこと」がコンセプトになります。最も単純なデザインで、高品質の硝材や部品を使い、仕上げをして、それで終わりです。これがシグマのデザインのコンセプトです。
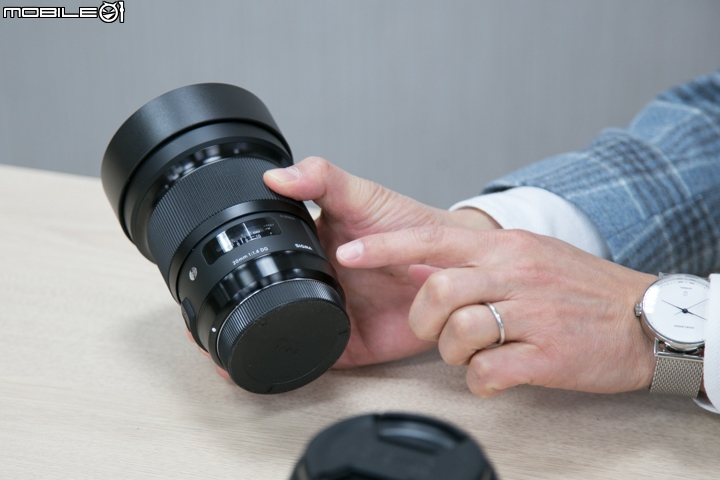
例えば、この金属の光沢部分にはとても精密な加工と酸化処理が必要になります。この金属部分には塗装はしていません。酸化処理だけで均一な仕上げをするには、加工がとても重要になります。製品が高品質であることを伝えるには、それぞれの部品の品質が重要になります。これはその一例ですね。
Q:デザインを担当しているのはシグマの社員なのですか?
A:いいえ、製品のデザインに関しては外部のデザイナーに頼んでいます。岩崎一郎氏です。もちろん、私達にも社内デザイナーがいますけど、コンセプトの核は彼が考えています。現行のSDシリーズは社内デザイナーによるものですけど、dp Quattroシリーズは岩崎氏が手がけました。
製品のデザインは工程が非常に複雑なんですよ。デザイナーが設計図を書き終わったとしても、それで完成ではありません。その図面を元に、工場とエンジニアが製品として生産可能かどうか議論します。その過程で多くのやり取りが必要なので、製品開発チームはデザイナーのオフィスと工場を行ったり来たりしないといけません。
Q:岩崎氏に製品のデザインを頼む時に、具体的にどのような話をしたのですか?
A:そんなにたくさん話したわけではありません。実は私たちは10年以上前からお互いをよく知っているんです。当時の彼の製品に感銘を受けて、お会いする機会があったのですが、その時にいつか将来一緒に仕事をしたいと話しました。ただ、それからしばらくは普通の友人のように付き合いを続けました。私たちは互いの考えをよく知っていますし、シグマの将来の方向性についても同じものを共有しています。なので、実際に新しいプロジェクトを開始する時にも、シグマの方向性やゴール、ビジョンなどを伝えただけで、デザインは全て彼に任せました。
なぜかというと、私はCEOですけど、ただのビジネスマンで、デザインの専門家ではないからです。CEOがデザインの細かいところまで首を突っ込むのは良くないと思っています。世の中にはこのことを誤解してデザインにあれこれ口出しするCEOがいるようですけど、これはデザイナーを混乱させるだけではないかと思います。なので、私はあえてデザインには口出ししません。岩崎氏はシグマについてよく知っていますから、彼を信頼するだけです。
会社について
Q:デザイナーに伝えた「シグマの方向性やゴール、ビジョン」というものが具体的にどのようなものなのか、お話いただけますか?
A:ここで簡潔に話すのは難しいんですけど、だいたい次のようなものです。
シグマは高品質な製品を作る会社でありたい。
シグマは革新的な会社でありたい。
シグマはユーザーに誠実な会社でありたい。
シグマは組織が最小な会社でありたい。
シグマは製品の価格が手頃な会社でありたい。
シグマは高級なブランドではなく、純粋に技術を追求した会社でありたい。
シグマを巨大な企業にしたくない。
Q:これらの目標はあなたの父も持っていたものですか?
A:そう思います。やり方は少し違いますけど、基本的な考えは同じですね。
Q:多くの会社はより強く、大きなものになろうとして、企業を買収したりもします。どうしてシグマは巨大になろうとしないのでしょうか?
A:私たちは非上場の会社です。株式を公開していません。未だに同族経営の会社です。なので、そもそも製品の回転率や売上、利益を上げていく必要がないんですよ。上場企業は株価を維持しなければなりませんから、それらの数字を伸ばしていく必要があります。しかし、シグマに関しては事業を継続することと、従業員の雇用を守ることが一番の目的になります。これはとても重要な事なんです。製品を作り続けること、ユーザーを幸せにすること、そして雇用を維持すること。そのためには、製品、売上、従業員、ユーザー、その全てのバランスを保つ必要があります。そして、そのために、会社が巨大である必要はありません。
もし売上を大きくすることが私たちの目標だとすると、賃金の安い海外に生産拠点を移すことになるでしょう。けれども、私たちは日本に留まることを決めました。一番の理由は高品質な製品を作る必要があるからです。もう一つは従業員の雇用を維持する必要があったからですね。普通、賃金の安い海外に工場を建設すると、最初は国内の工場と平行して生産を行います。そして、ある日突然方針を変えて、国内の工場を縮小し始めます。私達はこういうことをしたくはありませんでした。
シグマの工場は福島県の小さな町にあります。もしこの工場が閉鎖されると、地域社会に与える影響は甚大なものになります。私たちは従業員のみならず地域を守る必要がありました。これは理由の一つに過ぎませんが、いろいろな事情から私たちは急速に成長することを諦め、日本に残って、ここでしかできないことは何かを模索し始めました。シグマの製品が売れ筋のものからハイエンドへと変わっていったのも、このような理由があるからです。
Q:会社を急に大きくしたくはないと仰っていますが、シグマが徐々に成長していって、巨大になってしまったらどうしますか?もっと多くの製品を生産する必要に迫られた時、海外に新たに工場を建設しますか?それとも、それでも日本に留まるのでしょうか?というのも、キヤノンやニコン、ソニーといった会社は国内外の両方に工場を持っているからです。シグマがそれらの会社と同じくらい大きくなったあとでも、まだMADE IN JAPANにこだわりますか?
A:それは良い質問ですね(笑)今の時点では海外に工場を作る気は全くありません。けれども、将来もずっと日本だけで生産するかはわかりません。私たちの考えは、人件費が安いから海外に移る、ということをしないことです。それをし始めると、安い賃金を求めて世界中を回らなければならないですから。例えば現在も人件費が上がっている地域では、企業は生産拠点を他の国に移そうとしています。私たちはそのようなことをするつもりはありません。もし工場を構えるのなら、私たちは地域住民と共に生活をし、彼らを守りたいと思います。
今の時点では、私たちは地元の業者と協力して製造を行っています。私達はこれを「地域調達システム」あるいは「地域製造システム」と呼んでいるのですが、これは製造業では伝統的な手法です。しかし、今日では他の会社はとても大きな調達ネットワークを世界中に持っています。そのような会社は部品を最安値で調達して、最も人件費の安い場所で組み立てを行います。他はグローバルにやっていますけど、私たちはローカルにやっています。シグマと他の企業には大きな違いがあるんですよ。
私たちは、今までのやり方で高品質な製品を作ることはできます。けれども、私たちに馴染みのないグローバルなやり方を取り入れたとしたら、品質の維持が可能かはわかりません。なので、「工場を海外にも作るのか?」という質問に対する答えは「わかりません」です。
Q:社員に対して、特定のスペックのレンズを作るように指示したりはするのですか?
A:そうですね、よくやります。私は自分のオフィスを持っていません。本社の技術部の真ん中に小さな机があるだけです。そこでは150から160人の社員が働いていて、私から見て右側はカメラの開発チームがあり、左側にはレンズ開発チームがあります。私の机のすぐ隣は光学設計チームがいますので、そこのメンバーとよくやり取りをします。
それで私が「こんな感じのレンズ作ってよ」というと、たいてい「社長、アホですか」という返事が来ます(笑)。いつもこんな感じのふざけた会話をエンジニアとしてて、大変勉強になります。もちろん、エンジニアの方から「こんな製品を作りたい」という提案もあります。それが良さそうだったら実際にプロジェクトとして開始します。
Q:それも伝統的な日本の会社のやり方なのですか?
A:おそらく違うと思います。伝統的な日本のやり方は、手続きがもっと形式張ったものだと思います。まず、マーケティングと製品開発部が市場調査を行います。その後、開発計画が立てられ、製造可能かどうか製造部門が議論します。なので、新製品のアイデアはマーケティングと製品開発から出てくるのが普通です。
しかし、シグマの場合は、製品のアイデアは立ち話やエンジニアからの提案から出てきます。何が製造可能かということは、エンジニアが一番わかっているんですよ。開発部はわかりません。彼らはコンセプトを作るだけです。なので、エンジニアを自由にさせて、創造性を発揮できるようにするのはとても重要ですね。
日本では、会社の従業員を「サラリーマン」と呼びます。これは文字通り、毎月給料をもらっている人、という意味です。しかし、この言葉には否定的な意味合いもあって、単に上から命令されただけのことをする人、ということでもあります。そのような人は自由ではないし、創造性もありません。私は従業員に、熱心に仕事に取り組んで欲しいと思っています。
Q:オフィスの雰囲気はどのようなものですか?友人のように話したりするのですか?
A:そう願ってますけど、わかりません。直接彼らに尋ねてください(笑)。会社の雰囲気は官僚的ではなく、家庭的なものでありたいと思っています。社員がどのように感じているのかはよくわかりませんが、家庭的な雰囲気がオフィスにあればいいなと思います。
シグマ製レンズの品質の鍵がここに? A1システムの全貌を紹介する(その2)
(その1の続き)
以下はA1と開発者の石井氏の役割について、山木氏にインタビューしたものである。
デイブ・エッチェルズ(以下DE):石井氏はA1を設計し開発しただけでなく、レンズの製造工程にも関わっているのですか?
山木:そうです。実際に彼がA1の責任者に指名された時には、東京にある本社で光学設計者として働いていたのですよ。A1を生産現場で使用し始めた時、私は彼に会津に異動するよう頼みました。なぜなら生産能力を上げることは非常に重要だからです。そうでなければ、仮に良い設計をしても低い生産能力のせいで品質の基準を下げなければいけなくなります。私の理想は設計した数値に非常に近い品質基準を維持することです。開発ソフトによって導き出される理論値に、製造水準を引き上げたい。これは非常に困難なことですが、これが出来なければ高解像度カメラで使用されるレンズを作ることは出来ません。例えば8Kのようなカメラには非常に高性能なレンズが必要です。
DE:8Kというのは主に動画や映画で使われる概念ですから、そこに言及されるというのは興味深いですね。8000x4500ピクセル(3600万画素)の16:9や8000x6000ピクセル(4800万画素)の3:2がそれに当たります。
レンズ開発というのは、例えば設計者が「これが図面です」と言ってデータを開発部門に渡して、石井氏が「これ作るんですか。品質基準に合うようにどうやって作ろうかな?」と具体的な製造方法を決めていく、という感じなのでしょうか?
山木:そうですね。レンズの設計と同時に品質基準も決めています。製造前に試作品を作りますから基準をどれくらいにすれば良いのかわかります。
DE:許容範囲がどれくらいかもわかると。
山木:そうです。
DE:以前お話を伺った時に、製造困難という理由で工場がレンズの設計を拒否することがあると言われていたのを思い出しました。しかし、シグマでは工場が設計を拒否することはほとんどないとも言われました。実際に話を聞くまでは、そういうケースがあるという考えがそもそも私にはなかったんです。レンズ設計者が図面を渡して、工場がそれを見た後で「これを製造することは出来ない。こんなもの作る方法がない」と言って却下することがありえるのですね。
山木:石井はそういう役割も担っています。本部のレンズ設計者が設計を終えようとすると、その設計図は石井に送られます。彼はそれを見て、生産量に悪影響が出る要素がないか確認します。レンズ設計者も生産量を予測できますけど、石井はレンズの組み立てや部品の精度も調べます。そして工場がそれを製造できるかどうか判断するのです。
DE:つまり、彼はいわゆる感応度分析も行っているのですね。
山木:そうですね。感応度分析です。
DE:感応度分析というのは、設計された部品のそれぞれが許容範囲の最大値、あるいは最小値を取った時に、品質にどのような影響が出るのかを調べる作業を含みます。これは非常に骨が折れます。というのも、それぞれの部品が最大値・最小値を取った時の組み合わせを全てチェックしなければならないからです。調べる部品の数が増えれば確認しなければならない組み合わせは階乗的に増えていきます。もし部品が二つなら組み合わせは最大値と最小値のそれぞれを合わせて合計で4パターンになります。もし部品が3つなら2の3乗で8パターン。部品が10個なら1024通りもの組み合わせになります。レンズの場合、例えば控えめに12枚のエレメントからなるレンズでも、一枚のエレメントは二次元ではなく三次元的に考えなくてはならないし、回転することも考慮に入れなくてはいけません。非常に複雑な作業です。この分析を行って製造の判断をするにはレンズ設計と製造工程を深く理解していなければなりません。
石井氏は製造工程も理解していますから、「このエレメントは実際に製造するとこれくらいの数値になるだろう」ということが言えるわけですね。その後にシミュレーションを行い、製造に影響が出るかどうか判断をすると。
山木:そうです。しかし、工場が拒否するケースが増えると高性能なレンズが作れなくなって、面白みのない製品ばかりになってしまいます。こうした場合は彼が新しい企画を始め、製造能力を向上させたり、レンズ配置の新しい方法を考えたりします。
DE:ということは、設計図が来て、工場が「これは作れない」と拒否した時、石井氏が「これとこれとこれが原因でレンズが製造できない」と判断し、それを克服するための方法を考えるわけですね。
山木:そうですね。
DE:これはとても大変な仕事のように感じます。
山木:そうです。笑い事ではなく、設計者と工場の間の人間関係が円滑であることは非常に重要なんですよ。もし工場の人間が設計者を嫌ってしまったら、どんな設計でも拒否されてしまいますから。
DE:なるほど。「またアイツか・・・」みたいなことは起こって欲しくないですよね。
山木:社内がそういう状況になると、会社の状態も非常に危うくなります。本社にいる設計者と、工場の技師たちとの人間関係はとても大事なんですよ。
DE:ということは、石井氏は工場を代表して設計者とやり取りするような立場なのでしょうか?
山木:今の立場ではそうなりますね。特に彼はレンズ製造の開発に携わっており、特に光学性能の責任者です。彼の部署には他に機械部品を主に担当している社員もいます。
まとめ
かつては安価な初心者向けのレンズ製造で有名だったシグマだが、ここ数年で高性能レンズで世界をリードする企業に変貌を遂げた。るグローバルビジョンレンズは自社製のA1レンズ検査装置によって自動的に品質が検査されており、その中でも、50mm F1.4 Artや18-35mm F1.8はとりわけ大きな成功例と言えるだろう。高性能レンズには品質のばらつきが付き物だが、全数をデジタル的に検査されているグローバルビジョンレンズは、その品質においても業界随一なので、ユーザーは安心してよいと思う。
A1システムはシグマのレンズ製造において、もっとも重要な所有財産の一つだが、その詳細や、写真を読者に提供する許可を与えてくれた山木氏に感謝したい。
他のメーカーへ:私たちイメージング・リソースは所有財産に関する情報をこれまでも非常に慎重に取り扱ってきました。つきましては、貴社の製造工程を読者と共有する機会を提供したいと思いますが、いかがでしょうか?
シグマ製レンズの品質の鍵がここに? A1システムの全貌を紹介する(その1)
シグマの新しいグローバルビジョンラインのレンズの特徴の一つは、仕様通りの性能が出ているか全てのレンズの光学性能を機械で検査していることである。シグマはその検査装置を自社で開発した。シグマの一眼レフ、SD1に搭載されているフォビオンセンサーを、このセンサーとして使用している。この装置はシグマの生産工程の鍵であり、製品のばらつきが少なくなることによってユーザーにも大きなメリットがある。しかし、その詳細についてはずっと謎に包まれていた。
それが、今回初めて明らかになった。
2013年の8月に、私はシグマの会津工場を見学する機会を得て、そこで見たものを詳細なレポートにまとめた。私の知る限り、日本の生産ラインをあそこまで詳しくレポートしたものは過去に前例がない。工場見学のレポートで書いた内容が良かったからか、CP+2015のあとで会津を訪問した時、A1検査システムを詳しく見せて欲しいという私の願いを、シグマCEOの山木氏は聞き入れてくれた。そこで見聞きしたことを全て公開するわけにはいかないが、氏はA1の写真とその運用に関する説明を公表することを許可してくれた。
A1はとても興味深いシステムだ。生産ラインから流れてきたレンズの全てをA1で検査しているというのは驚くべきことである。いくつかのカメラ・レンズメーカーは製品の一部を100%検査していると思うが、多くの検査は光学投影方式で行われているので、合格か不合格かの基準は検査する人間の判断によってわずかに変化する可能性がある。それに対してA1では、許容範囲はMTFの数値によって絶対的に決められており、レンズの撮影範囲内を複数箇所検査することによって合否が判断される。私の知る限り、このような方法でレンズを検査しているのは業界でもシグマだけである。
以下の記事ではA1システムの写真やその構造、運用方法を紹介していく。驚くべきことに、シグマはこの時点で60台以上のA1を生産ラインで使用しており、現在も新しいA1を作り続けている。A1をゼロから始めて一つ完成させるのに2週間ほど時間がかかるそうだが、同時に2台以上A1を開発できるかどうかは不明である。
これはA1とその開発者である石井正俊氏の写真である。石井氏はA1を開発する前はシグマの本社でレンズ設計者として勤務していた。A1の稼働開始以降は会津若松に異動し、工場とレンズ設計者の橋渡しをする仕事をしている。
これがA1の全体写真である。写っているのはA1の開発者である石井正俊主任。彼は生産技術部に所属している。A1システムは標準的な傾斜エッジターゲットを使って撮像範囲の複数箇所でMTF値を測定している。中央と周辺とでは異なった数値が基準として設定されている。また、サジタル方向と軸上方向の数値の比も測定される。5つの測定箇所のうちどれか一つでも基準を満たさなかったり、全体的なMTF値が不足していたり、サジタル方向と軸上方向の数値に差がありすぎたりすると、そのレンズは調整に戻される。もし、調整しても基準を満たさなければ、そのレンズは破棄される。
なんてもったいない!と思われるかもしれない。十数万円ものレンズが、周辺の画質が基準よりちょっと甘いというだけで破棄されるのだ。これが機械による全数検査に伴う強みであり、悲哀でもある。コンピュータは「このレンズはほんのちょっと足りないだけだから目を瞑って通過させてやるか・・・」などということは絶対に言わないのだ。合格か不合格か、2つに1つしかない。
シグマはA1以前にもコンピュータを使用したMTF装置を使用していたが、そのセンサーは解像度が低いわりに高価なコダック製のものだった。山木社長も石井氏もそのセンサーの具体的なスペックを覚えていないそうだが、センサーサイズはAPS-Cよりも小さかったという。従って、フルサイズ用レンズを検査するためには5つのセンサーを撮像範囲内に配置する必要があった。また、そのセンサーはベイヤータイプだったので、現行のA1で使われているフォビオンセンサーよりも空間解像度が低かった。
シグマはこれまでに生産した全てのグローバルビジョンのレンズの検査結果をデータベースに保存しており、このデータには全世界のカスタマーサポート部のスタッフがアクセス可能である。したがって、もしあるユーザーが「左側のピントが甘いんだけど」と連絡してきたら、サポートはデータを調べて製造時点での数値から経年変化による劣化なのか、それとも使用中、あるいは輸送中に何かがあったからなのか、判断をすることができる。
個人的に実際に検査で撮影した画像も保存しているのか気になった。長期的な生産性の分析に役立つのではと思ったからだが、シグマによると画像は保存していないという。測定数値を記録しておくだけで十分だそうだ。
A1システムの端末部。キヤノンマウントの24mm F1.4 Artレンズが装着されている。容易に想像がつくことだが、このシステムに求められる部品の精度は極めて高い。装置全体は分厚い金属の板で作られている。レンズの下からぶら下がっているケーブルはマウントを経由して本体とつながって情報をやりとりしている。
私が特に興味深いと思ったことは、A1が最適値を中心にしてフォーカスをブラケットさせて検査をしていることだ。このことによって、偏心しているかどうかを調べることができる。まず最適なフォーカスで撮影し、その後、バックフォーカスとフロントフォーカスの撮影をすることで、偏心が発生しているか確認できる。最適なフォーカスで撮影をすることで、設計通りの数値が出ているかどうかは確認できるが、さらにフロントフォーカスとバックフォーカスを調べることで、レンズの性能が全体としてどうなのか、判断することができる。もちろん基本的には、画像の両端の数値が大きく異なっていれば、偏心が発生している証拠にはなる。これは、特に説明を受けたわけではないが、ある部分のフォーカスの問題から、どのレンズエレメントに問題があるのか判断できるのではないかと感じた。
ズームレンズの場合は、A1はズームの両端の数値だけを測定している。これは、レンズの両端で数値に問題がなければ、その中間で問題が発生することはほとんどないことが理由である。
以前にも言及したように、A1はレンズの性能を測定するのにAPS-Cサイズのフォビオンセンサーを使用している。フルサイズ用のレンズを測定する時には、超高精度で動作する機械部がセンサーを動かして、フルサイズ用の撮像範囲をカバーする。下の動画はセンサーが動く様子を撮影したものだ。
フルサイズ用の撮像範囲をカバーできる
グローバルビジョンの誕生とともにA1が使われるようになってから4年が経過した。石井氏によると、最初にA1のアイデアが浮かんでから開発が終わるまで1年かかったという。A1の開発で最も困難だったことの一つは、SD1のセンサーがAPS-Cサイズだったことだという。しかし、検査装置がフルサイズをカバーすることは絶対条件だった。そのためには、フルサイズ用の撮像範囲を中央から周辺まで、センサーを配置した基板を動かす必要があった。石井氏は詳細までは説明しなかったが、許容範囲の非常に小さい精密な部品を使って装置を組み立てることで、完璧な平面移動を達成するというのが基本的な考えだ。シグマは既に1ミクロン以下の違いを測定できるデジタル検査装置を持っていた。A1のセンサーを動かす制御部分を組み立てた後で、それを検査装置の中に入れ、完璧な平面が出るように微調整を行うことが出来た。
A1センサーユニットの前にあるのがレンズが取り外された状態のキヤノンEFマウント用アダプター
APS-C用レンズの検査には約40秒かかるが、フルサイズ用はセンサーをフルサイズ用に移動させる必要があるので60秒から65秒かかる。個人的にフルサイズ用でもそれほど多くの時間がかかるわけではないことを知って驚いた。
これはニコンF用のアダプターである。アダプターはステンレス鋼で出来ており、がっしりとした作りのマウントを介して、検査装置に取り付ける。レンズアダプターは基準値に完璧に合うように作られており、センサー基盤もマウントに完全に水平になるように配置されている。これは以前会津工場を訪問した時に撮影したものによく似た並行を検査する装置によってチェックされている。
A1システムは複数のレンズマウントに対応しなければならない。また、マウント形状だけではなく、焦点距離や絞りなどの情報をやり取りする電気信号にも対応していないといけない。これを解決するために、A1装置そのもののフランジバック、つまりマウントの先頭からセンサーまでの距離は、非常に短いものとなっている。そして、そのA1のマウントに、各レンズ用に長さや電気系統を変えたマウントアダプターを装着する。
上の写真で石井氏の手にあるのがニコンFマウント用のアダプターである。この写真ではマウントがA1に取り付けられている。リボン状のケーブルはA1の制御装置と繋がっており、コンピュータがレンズと情報をやり取りするのに使われる。
この写真はA1のモニターの一部分を撮影したものである。財産権の関係でスクリーンの右側が写っていないが、そこにはMTFの数値と、検査されているレンズが基準を満たしているかどうかが表示されている。A1には2つの動作モードがある。一つは、製造用で、生産工程から上がってきたレンズを素早く検査するのに適している。もう一つは研究開発用で、フレームの中の任意の場所で、様々な種類の検査をすることができる。
A1には研究開発用のモードがあるという話を聞いて、レンズ開発におけるA1の役割がどのようなものなのか疑問を抱いた。A1を使うことでレンズ設計ソフトでは見つからないような問題が明らかになるのだろうか?もしそうだとしたら、シグマの光線追跡用のソフトはモデリングが十分ではないか、あるいは試作品を使って実際に測定する必要があるのだろうか?
シグマによると、設計ソフトがレンズの性能をシミュレートできないというわけではなく、工場で生産されたものが、設計上の水準をどれだけ満たしているのかを調べる必要があるのだという。言い換えると、ソフトで設計された数値を確認するのが目的ではなく、ガラスや金属、プラスチック部品のそれぞれが、どれだけ正確に要求を満たしているのかを検査しているのだ。
シグマCEOの山木和人氏は、会津若松にあるシグマの工場がシグマの成功の鍵を握っていると考えている。山木氏とその父は何年も前に、部品供給網全体を日本に置くという戦略的な決断をした。これは一部の生産コストの上昇に繋がるが、工場の従業員の技術レベルを高いままで維持することが出来、部品供給元の品質管理を高いレベルで行うことができる。山木氏によると、シグマに就職した社員のほとんどは他社に行くことがないという。グローバルビジョンラインのレンズのように高スペックのレンズを作るのには従業員の技術が必要不可欠であり、シグマは高性能レンズに必要な高い製造能力と開発能力を備えている。
今回の訪問でもっとも重要なことだと私が感じたことは、シグマはレンズ設計者と工場の生産現場との距離をできるだけ近くするよう、多大な努力をしている、ということである。その例の一つ、A1システムの開発者である石井氏は、元々はレンズ設計者であった。彼はA1の開発後に会津に異動し、工場と本部の開発者との調整役として働いている。
シグマCEOの山木氏は、レンズの性能がソフトで設計された理論値にできるだけ近づくよう工場に働きかけているという。A1システムが欠陥を見つける度に、シグマは生産工程を見なおして、より良い製品を作るよう改善を続けているのだ。
CP+2015 シグマインタビュー「大きな工場・小さな事業所」(その2)
(その1の続き)
―シグマの24-105mm F4が製造終了になったという噂が以前ありました。この噂はもちろん真実ではなかったですが。このレンズは期待した通りの性能になりましたか?
山木:私自身は標準ズームとしてこのレンズの性能に満足しています。標準ズームというのは広角から標準、望遠までカバーしているので設計が一番難しいものなんですよ。特に望遠と広角とでは、求める設計が全く異なります。従っていくつかの面である程度妥協せざるを得ませんでした。
24-105mmは標準ズームとしては良い性能になったと思っています。市場に出ている他のレンズと比べて突出しているというわけではないんですが、まあ十分良いだろうと。生産終了の噂が出たのは、十分な数を供給することが出来なかったからです。最初にこのレンズの需要を予測したのですが、私たちとしてはそれほど売れないだろうと判断し、大量に生産できる体制にはしなかったのです。しかし、ある時点で在庫が全て売り切れてしまい、突然大量の注文を抱えることになってしまいました。しかし、そこから生産を再開できるまでには4ヶ月かかります。
―このレンズのように需要が比較的少ないレンズは、順番に特定の期間だけ生産していくということなのでしょうか?
山木:そうです。人気のある35mmや50mm、売れ行きの良いズームレンズなどは通年で生産をしています。しかし、余り売れ行きの良くないレンズの場合は3ヶ月間、あるいは4ヶ月間といった一定の期間だけ生産しています。
シグマのアートシリーズのF1.4単焦点は現在24mm、35mm、50mmの3つの焦点距離からなる。35mmと50mmは圧倒的な光学性能を持つが、24mmもこの流れに乗った高性能レンズになると予想される。
―シグマは高性能を追求していますので、結果としてレンズのサイズは大きくなります。例えば品質とサイズを妥協したレンズを作ることに興味はありますか?
山木:それはコンテンポラリーラインですね。このラインのレンズは大きさ、重さ、値段、性能のバランスを取ったものです。もちろん安かろう悪かろうみたいな製品ではありませんが、どこかで妥協点を探ろうとしています。アートシリーズはまず性能が最優先です。サイズや重さ、値段はその次です。
―例えばソニーのFEマウント用ツアイス55mm F1.8などは小型軽量で性能も申し分ないです。もしアートシリーズをこのマウント用に作るとするなら品質とサイズのバランスが異なった、例えばより小型のレンズを作る可能性はありますか?
山木:そうですね。そのような製品を作ることに興味はあります。しかし、私たちがレンズを作るのは他社の製品と異なった新しいものを作りたいから、という理由もあります。ソニーが既に小型で手頃な価格の55mm F1.8を作っているのだとしたら、どうして同じものをもう一つ作る必要があるのでしょうか?しかし、例えばですがF1.4とF1.8には大きな違いがありますから、私たちが作るならF1.4にするか、全く別の何かを作るかでしょうね。
―アートシリーズの次はどのような製品になりそうでしょうか?
山木:基本的な方針は、可能な限り最高の性能を、ということです。もう一つの目標は、これまで市場に存在していなかったような、全く新しい製品を作ることです。例えばですが、キヤノンの11-24mmは衝撃的ですね。性能も素晴らしいです。値段もかなりしますけど。
キヤノンの11-24mm。世界初の11mmをカバーするフルサイズ用広角レンズ。シグマは広角ズームという領域にもう一度チャレンジするつもりのようだ。
―シグマがグローバルビジョンのレンズに超広角ズームを入れる可能性はありそうですか?
山木:そうですね。そうしなければなりません。私たちは広角ズームのパイオニアであると自負しています。70年台にシグマが作った21-35mmは世界初の広角ズームだったと記憶しています。その後も18-35mm、17-35mm、15-35mm、12-24mmと開発を続けました。シグマは常に広角ズームの記録を更新し続けてきたのです。しかし、キヤノンはシグマのスペックを超えました!私たちは新しい製品を投入する必要があります。
―多くの広角ズームは前玉のサイズもあってフィルターを付けることが出来ません。これは問題だと捉えていますか?それともフィルターの重要性は下がってきているのでしょうか?
山木:いや、フィルターは大事です。私たちとしてもフィルターを装着できるレンズを作りたいと思っています。しかし、物理的に難しいことが多いです。光はとても広い角度から入ってきますから。しかし、ユーザーはフィルターが装着できたほうが良いと考えているでしょう。
―ユーザーから次のアートシリーズはこうして欲しいという要望は来ていますか?
山木:一番多いのが24-70mm F2.8ですね。その次がマクロ、そして14-24mmといった広角ズームです。
―シグマは10年後にどのような会社になっていると思いますか?
山木:未来を予測するのはとても難しいですね。しかし、写真は100年以上もの歴史がありますから、仮に市場が縮小したとしても写真愛好家は10年後もいるだろうと思います。なので、シグマはそういった愛好家やプロの写真家のために高性能なレンズを作っているでしょうね。
【編集後記】
私たちdpreviewは機会があるごとに山木氏にインタビューするようにしている。というのも、氏のカメラ産業に対する見識や、困難に直面していることを認める率直さは、経営者のコメントとしては非常に稀だからだ。
このことの理由の一つに、氏がシグマという稀有な会社のCEOであることも影響しているだろう。比較的小規模な同族経営の会社であり、材料を国内から調達し、国内の工場一箇所だけで生産している。これまでのインタビューで山木氏は、現在の品質を維持できないほどの規模まで事業を拡大する気は全くないと宣言してきた。このCP+でのインタビュー後に私自身も会津工場を訪問する機会を得たが、先代の言う「大きな工場・小さな事業所」哲学を実際に目にすることが出来た。2011年の大震災の後で、シグマは地震の僅か二日後に限定的ながらも生産を再開することが出来たが、これもシグマが材料の調達先を地元を中心に行っているからだろう。他の会社はもっと複雑な仕入れ方法を採っているので、通常の生産体制に戻るまでにもっと多くの労力が必要だった。
シグマは、しかしながら、別の意味で高級ブティックのような会社と言える。シグマのレンズの中には需要がとても多いものがあるにも関わらず、生産量を増やすことをしていないからだ。山木氏は新型の24mm F1.4は現在の市場で最高のレンズであると自信を持っていたが、私自身その言葉を疑う気はない。しかも、市場価格で10万円を切る。このレンズの需要はたいへん大きなものになると予想される。シグマが今後も多くのレンズを開発し、販売していくのだとしたら、シグマは今まで以上に生産能力を拡大する必要に迫られるだろう。しかし、そうなると山木氏の「大きな工場・小さな事業所」哲学を維持していくのは困難になるのではないだろうか?その結末がどうなるのかは、その時が来ないとわからないだろう。
これまでのインタビューからも、山木氏は長期的な視野で物事を判断していることがわかる。正直言って、シグマのカメラ事業が赤字だという話を聞いても私自身全く驚きはなかった。しかし、カメラ事業を継続する理由には感銘を受けずにはいられなかった。シグマのdpシリーズの強みは、その圧倒的な高画質である。そのようなカメラを作る経験が、シグマの交換レンズの性能向上に寄与していることには、疑問を挟む余地はない。それはセンサーについても同様である。カメラ市場ではフォビオンセンサーは一般的なベイヤーセンサーに全く太刀打ち出来ていないが、シグマカメラのファンには受け入れられているし、シグマは自身でフォビオンを搭載した「A1」MTF測定器を開発することが出来た。
このインタビューから何を知ることができるだろうか?一つは、シグマが自社の哲学 ― 会社運営やマーケティングよりも技術開発に価値がある ― に依然として重きを置いているということである。二つ目は、シグマは今後も売れ筋商品やOEMではなく、高性能レンズに注力していくということである。また、市場に存在していない全く新しいレンズを今後も開発していくということだ。三つ目は、より利益の出る製品であるレンズの性能向上に役立つのなら、シグマはカメラ事業が赤字であっても気にしないということである。
CP+2015 シグマインタビュー「大きな工場・小さな事業所」(その1)
元記事:CP+ 2015 Sigma Interview - "small office, big factory"
今年(2015年)のCP+ではシグマを含む主要なカメラ会社の重役たちにインタビューする機会を得た。今回のインタビューではシグマCEOの山木和人氏に、高画素化時代におけるレンズ生産の課題、シグマの「大きな工場・小さな事業所」という哲学、シグマ製カメラの開発を続ける理由、などについて話を聞いた。
山木:可能な理由はいくつかあります。まずシグマは比較的規模の小さな企業です。従って、大きな会社と比べて経営に必要な人員は少なくて済みます。これが父の「大きな工場・小さな事業所」哲学です。つまりシグマは会社運営そのものを非常に少数の、無駄のない人員で行い、大量のエンジニアチームを持っているということです。
私も父の方針を引き継いでいますから、シグマの運営に関わるコストは非常に少なくなっています。これが一つ目の理由ですね。二つ目の理由は私たちは生産をほとんど自社の工場で行っているからです。もし他社から部品を仕入れたらそのコストを支払わなければなりません。シグマは可能な限り全部を自分たちでやろうとしています。
―シグマは売れ筋商品よりはハイエンドな商品により集中しているのでしょうか?
山木:経済的な理由でシグマはハイエンドな商品に集中する必要があります。私たちはすべてのレンズを日本国内で生産しています。円は以前よりも安くはなりましたが、依然として中国や他のアジア諸国で生産するより製造コストは高いです。しかし、これはハイエンド商品を生産する理由の二つ目なのですが、単に売れ筋商品を作るよりも、ハイエンド商品を作ったほうが喜びが大きいからなんですよ。
―ハイエンド商品を作ったほうが利益が大きいのでしょうか?
山木:それはものによりますね。例えばいくつかのハイエンド商品の利益率はあまり大きくはありません。売れ筋商品との一番大きな違いは、ハイエンド商品に高い価値を付与すると、消費者がそれを受け入れてくれて対価を払ってくれるということです。それに対して売れ筋商品で最も重要視されるのは、単にどれだけ安いか、ということなんです。
―シグマは高級でプレミアムなブランドになろうとしているのでしょうか?
山木:私の夢はシグマをそういう意味での高級ブランドにすることではありません。シグマは高品質な商品を手頃な価格で提供する会社でありたいと思っています。しかし、品質に関して言えば答えはイエスです。シグマは高性能な製品を作る会社だと認識されたいですね。
―過去には作れなかった高性能な製品を作ることができるようになった技術的な革新みたいなものは何かあるのでしょうか?
山木:数十年前と比較したら、当然のことながらコンピュータの発展が大きいですね。光線の動きをトレースする計算時間がはるかに短くなりました。その結果、設計者が何通りもの光線のパターンを試せるようになったのです。私が入社した頃は一つの計算に30分かかっていたものが、現在では1分以内でできます。これが最も大きな違いですが、これは他の会社でも同じことです。
会津にあるシグマ設計部の技術者。コンピュータで新しいレンズの設計を行っている。
もう一つの要因はシグマの工場です。私たちの工場はレンズ研磨について言えば、とても高い生産能力を持っています。レンズ設計というのは常に制限との戦いなんですよ。例えばサイズや重さなどのスペック的な制限だったり、手ブレ補正を組み込む必要があったり、工場の生産能力だったりします。
例えばあるレンズの形状が工場で研磨ができないものだったら、その設計は諦めなければなりません。しかし、シグマの工場は高度な生産能力を持っていますから、複雑な形状であっても生産することが可能になります。
―シグマが設計にコンピュータを使い始めたのはいつ頃なのでしょうか?
山木:私もわからないのですが、かなり昔のことだと思います。おそらく30年前とかそれくらいでしょう。当時のコンピュータは計算にとても時間がかかったので、導入したことで状況が一変したということはなかったようです。当時の設計者は良いレンズを作るのに直感と経験に頼っていました。それゆえ、異なったレンズを設計するのにも、既存のレンズの設計を元にするなど、決まったやり方に従わざるを得ませんでした。しかし今日では計算がとても速いので設計者はあらゆる方法を試して実験することが出来ます。
また、現在の設計者は過去の設計を参考にすることも出来ます。カメラ産業にはレンズ設計に関する巨大なデータベースがありますから、あるレンズを作ろうとしたら、どの設計が向いているのか、あらかじめ調べることが可能です。
―シグマは異なるマウントに向けてレンズを生産していますが、ピント精度の問題にはどのように取り組んでいるのですか?
山木:私たちはカメラのファームウェアを変えることは出来ませんが、レンズのファームを変更することが出来ます。ユーザーがボディとレンズをシグマに送ってもらえれば、私たちの方でピントを調整することが可能です。しかし、これには時間がかかるので多くのユーザーが敬遠しがちです。その代わりとして、USBドックによるピント調整ができるようになっています。例えばカメラボディでピント調整をすると、焦点距離や被写体との距離にかかわらず全て同じ変更が適応されます。しかし、USBドックを使えば被写体との距離や焦点距離に応じてそれぞれ最適な調整が可能になります。
―ちゃんと調整すればピントはものすごく良くなるんですが、例えば被写体との距離が4ヶ所、焦点距離が4つだとすると、合計で16ものパターンでそれぞれのピントを合わせなければなりません。これはかなり大変です。シグマではこの調整を自動化したり、補助機能をつけたりする予定はありますか?
山木:それは簡単ではないですね。もちろん、ユーザーの中にはこのやり方を好まない方もいるでしょうから、もっと良い方法を提供しなければならないと考えています。ピントに問題があるユーザーには、まずカスタマーサポートに連絡を入れて欲しいです。サポートの方でピントを調整できますから。
―レンズ設計で最も困難なことは何でしょうか?
山木:様々な困難がありますが、現在の最大の問題はカメラの高画素化ですね。画素数は将来的にもっと増えていくと思いますが、高画素化時代に対応していける会社はそれほど多くないと思います。
キヤノンの新型5Dsと5DsRは5000万画素センサーを搭載している。
山木氏によるこのカメラで使うことが厳しいレンズは相当数に上るという。
山木:そう思います。もちろん絞りにもよると思いますけど。しかし、シグマの新型24mm F1.4レンズは現在市場に出ている同焦点距離のレンズの中で最高の性能であると自負しています。もしこのレンズが5Dsで使えなかったら、他に使えるレンズは世界中どこにもないということです。
―シグマのA1システムについて教えて下さい。
山木:A1はシグマが独自に開発したMTF測定器です。これは内部にフォビオンセンサーを使用しています。A1を開発する前は市販のセンサーを使用したMTF測定器を使用していましたが、これはレンズの検査に必要なだけの解像度がありませんでした。そこで、フォビオンを使用した測定器を開発しました。現在では全てのグローバルビジョンのレンズがA1で検査されています。
山木:それはないですね。私たちはミラーレス用のレンズラインナップを増やしたいと思っています。単に優先順位の問題です。
―現在の優先順位について何か教えてもらえますか?
シグマの新型dp0は焦点距離21mmのレンズを持つ。山木氏によると、カメラj事業が赤字でも開発によって得られる知識と経験が、交換レンズを開発する時に非常に貴重なものになっているという。
―先ほど言及されましたフォビオンに関連した話なのですが、シグマはつい先日、新しいDPシリーズのdp0を発表しました。正直に言うとシグマのカメラは売れ筋商品であるとは言い難いと思います。現在のニッチなカメラであるという状況に満足されていますか?それとももっと多くの人に売れるようになってほしいのでしょうか?
山木:単にビジネスとして考えると、もちろんもっと売れて欲しいですね。しかし、私たちはシグマのカメラのユーザーがどういう人達なのかよくわかっています。他社のカメラとは異なったカメラを作らなければなりません。もしシグマのカメラが他のメーカーのものと似たようなものだったらユーザーにとってメリットは何もないですから。シグマのカメラを使ってる人たちというのはそれほど多くはありませんが、彼らが求めるものをわたりたちは理解しているつもりですし、そういう意味ではdp0というのはシグマユーザーにとって完璧なカメラだと思います。私たちの優先順位は既存のシグマユーザーが欲しがるような製品を作ることです。ユーザーの数を増やしていくのはその次ですね。
―レンズ事業と比べてカメラ事業でどれほど収益を上げているのか教えてもらえますか?
山木:カメラ事業は全く利益を生み出していません。特にセンサーの開発には多大な費用がかかりますから、それを計算に入れるとカメラ事業は常に赤字です。厳密にビジネス的な観点で見ると、カメラ事業をやるメリットはありません。しかし、主に二つの理由から出来る限りカメラ事業を続けていきたいと思っています。
一つ目の理由は、カメラメーカーになるということが私たちの夢だからです。これは父が長年追い求めていた夢でもありました。二つ目の理由は、カメラ事業を続けることで多くの技術的な知識と経験を蓄えることができるからです。これが良いレンズを作るのに大きな助けになります。私たちのカメラは現在市場に出ている中でも最も高解像度のカメラの一つですから、そのカメラの性能を満たすために高解像度のレンズを作る必要があるのです。このことが結果として他マウント用レンズの性能向上にもつながります。また、センサーの画像処理用に独自の画像処理エンジンを作る必要があったのですが、その経験があったので独自のMTF測定器の開発もできました。
―ということは、最近のシグマレンズの高い性能というのはカメラ開発の賜物であるということでしょうか。
山木:そうです。カメラを作ることによって、あのような高性能レンズを開発することができるようになったと思います。ビジネス的な観点で見たらカメラ事業に意味はないかも知れませんが、メーカーとして必要な技術的知識・経験を蓄えるためと考えると、完全に理にかなっています。
シグマCEOインタビュー:なぜマイクロフォーサーズのレンズは少ない?フルサイズフォビオンは実現可能?(その3)
dp Quattoroの持ち方に悩んだことはないだろうか?これが正しい持ち方だ!
IR:私たちの編集者からまた質問です。以前のインタビューでDPシリーズにズームは出ないのか尋ねました。その時の返事は、サイズが非常に大きくなってしまうので現実的ではないということでした。しかし、現在のdp Quattroシリーズは、ボディそれ自体が非常に大きくなっています。ということで、クワトロはもうボディが大きいのだからステップズームのようなレンズは出来ないのでしょうか。それとも、やはり画質を優先すると単焦点しかないのでしょうか。
山木:それは確かに正しいですね。今のクワトロはボディが大きくなっていますから、大きなレンズになっても大丈夫だと思います。クワトロは右手でグリップを握り、左手でレンズの下部を支える形になっていますから。
IR:確かに両手で持つ設計になってますね。
山木:なので、クワトロのレンズは大きくなる余地はあります。ただ、問題なのは画質です。とても高性能なズームレンズを開発しないといけないですから、これは難しいと思います。
IR:確かに、レンズはセンサーの解像度に合わせないといけないので、とても高い性能が必要ですね。
山木:特に標準ズームレンズは難しいです。広角ズームだったらまだ大丈夫なんですが。
IR:広角のほうが容易なのですか。標準ズームだと・・・
山木:高性能を発揮するのは非常に困難です。
IR:さて、とても興味深い150-600mmレンズが発表されました。しかも同じスペックで2本になります。150-600mm F5-6.3 DG OS HSM Sportsが定価26万円、そして150-600mm F5-6.3 DG OS HSM Contemporaryが、これはまだ値段は発表されてませんね。だいたいどれくらいになりそうですか?
山木:まだ決めていません。しかし、とても手に入れやすい価格になると思います。このレンズは、元々一つのプロジェクトから開始したんですよ。
IR:そうなんですか?
2008年発売の150-500mm F5-6.3 APO DG OS HSM
このレンズの後継機は2種類発売され、望遠端も伸びている
山木:これは以前発売していた150-500mm F5-6.3 APO DG OS HSMの後継機種にあたります。この望遠端を600mmまで伸ばすことが最初の目標でした。私の記憶では2年前に開発を開始したと思います。
その時設定した目標は、まず高画質を達成することでした。特に色収差を最小限に抑え、同時に600mmを達成することを目指しました。二つ目の目標は、ハイアマチュアやプロ写真家に向けて、防塵防滴性能を備えた鏡筒を作ることでした。そして、最後の目標が150-500mmと同じくらいの、比較的軽量でコンパクトなレンズにすることでした。この三つの目標を妥協する気はなかったのですが、研究をするにつれて、何かを犠牲にしなければ目標を達成するのは不可能だという結論に至りました。
最終的に、このプロジェクトを二つに分けることを決断しました。スポーツラインは大きく、重く、高価になりますが、最高の画質と性能の高い鏡筒を備えたレンズになりました。そして、コンテンポラリーラインのレンズは軽量でコンパクトながらも、良い画質である、そういうレンズを目指しました。
IR:なるほど。開発の段階で、もし3つのゴールを全て達成しようとしたら非常に高価なレンズになってしまうとわかったのですね。さらに、もし画質を再優先するのなら、レンズが重くなってしまうのは避けられないと。
山木:実際には、この二つのレンズは画質でもそれほど差があるわけではないんですよ。特に中央の画質にはほとんど違いはありません。違いを見分けるのは非常に困難だと思います。しかし、望遠端で周辺の画質を比べると、スポーツラインはコンテンポラリーと比べて軸上色収差がわずかになります。
IR:ということは、画質の違いは600mmの周辺に出る軸上色収差だけだと。
山木:レンズの設計というのは非常にデリケートなのです。望遠端の周辺の収差という一点だけを改善したくても、それだけでレンズが巨大になってしまうのです。
SIGMA 150-600mm F5-6.3 DG OS HSM Contemporary
スポーツラインと比べて軽量で価格も抑えてある
IR:特にこのレンズはエレメンツも多いですから、全てコントロールするのは大変でしょうね。
山木:そうですね。
IR:しかし面白いですね。この二つは解像度の点ではほとんど同じで、軸上色収差の違いだけだと。しかし、軸上色収差そのものはソフト的に処理するのが容易だと思います。シグマはAdobeにレンズプロファイルを提供していますよね。
山木:確かにそうです。けれども、やはりユーザーは性能の良いレンズを欲しがるんですよ。なので、私たちもそれに合わせないといけません。
IR:なるほど、わかります。私も高性能レンズが必要ないと言うつもりではありません。しかし、高価なレンズが買えない人でも、コンテンポラリーラインで十分な高画質を得られるわけですね。
別の見方をすれば、画像処理の手間を惜しまなければ、高性能で軽量なレンズが手に入る、ということでもあります。周辺画質だけをあとから処理すればいいのですから。
もう一つの質問は18-300mm F3.5-6.3 DC Macro OS HSM Contemporaryです。これはシグマ、ニコン、キヤノン、ソニー・ミノルタ、ペンタックスの各マウント用に開発がアナウンスされています。これがソニーのEマウントやマイクロフォーサーズ用に発売される可能性はあるのでしょうか?
山木:ありません。というのも、そのレンズは従来の一眼レフ用に設計されているからです。もし、ミラーレス用に発売するのならフォーカス方式を変更しないといけないので、光学設計から変えなければなりません。
IR:先ほども話したように、ライブビューだと違う方式を取らなければいけないのですね。
山木:そうです。ミラーレス用だとステッピングモータか、ボイスコイルモータに変更する必要があります。
IR:興味深いですね。
山木:ミラーレスでは、AFの動作中は常に被写体を追い続けていないといけないんです。フォーカスの合う場所を探して常に前後に行ったり来たりするので、常にレンズが動いています。そのために、フォーカス用のレンズはとても軽量である必要があります。
IR:AF速度を早くするために軽くないといけないのですね。
山木:そうです。また、トルクが強くてサイズの小さなモータというのは、それほど多くはありません。やはりレンズを軽くしないといけないのです。
IR:なるほど、非常に軽量にしないといけない。そうなると、レンズ設計そのものが全く別のものになるわけですね。
山木:全く違います。
IR:動画に向けて光学設計を変えるとより高価になるのでしょうか?それとも、画質が犠牲になるのですか?
山木:値段が上がるわけではありません。単純に全く別の設計や製造方法に変わるだけです。
IR:18-300mmのミラーレス用が出ないことを考えると、それを作るのにコストがかかるか、製造が難しいのでしょうね。とても面白いです。
さて、これは個人的な感想なのですが、クワトロのアップデートの頻度と速度にはとても感銘を受けました。私たちがクワトロの画質に問題を見つけたすぐあとで、シグマはそれを改善するアップデートを行いましたね。
山木:実を言うと、問題のほとんどはバグだったのですよ。なので、製品の出荷前に修正されてしかるべきでした。恥ずかしい話です。
IR:バグは修正されましたけど、今後もクワトロのアップデートは行われるのですか?
山木:はい。クワトロの改善は今後も行っていきます。
IR:ユーザーから要望が色々出てると思いますけど、そういうのも実装していくのですね。
山木:そうですね。
IR:この件についてはもう少し話をしたいのですが、残念ながら時間が来てしまいました。今日はとりあえずここで終わりたいと思います。ありがとうございました。
山木:ありがとうございました。あなた方と話をするのはいつもとても楽しいんですよ。技術的な話が多いし、詳しいですから。他のインタビューとは全く違う面白い質問が多いです。
IR:そうなのですか?とても光栄ですね!
シグマCEOインタビュー:なぜマイクロフォーサーズのレンズは少ない?フルサイズフォビオンは実現可能?(その2)
IR:読者から別の質問が来ています。「シグマのAPS-C用のコンテンポラリーとアートラインのレンズをマイクロフォーサーズ専用で出さないのはなぜですか?」
APS-C用とマイクロフォーサーズ用とではそもそもセンサーのサイズもバックフォーカスも違いますよね。しかし、マイクロフォーサーズ専用レンズの可能性はあるのでしょうか?既存のレンズをマイクロフォーサーズ専用に作り直すといった要望はあるのですか?
山木:今のところ、それほど大きな要望はありませんね。確かにいくつかのレンズはマイクロフォーサーズ専用に作ったほうが良いと思います。シグマの使命は高性能なレンズを手頃な価格で提供することですが、この場合は需要の大きさがとても重要になります。例えばAPS-C用とマイクロフォーサーズ用を同じ設計で作ったら価格を下げることが出来ます。しかし、マイクロフォーサーズ専用のレンズを作ると、どうしても価格は高くなるでしょう。設計を複数のマウントで共有することで、私たちはレンズの価格を下げることができるのです。
IR:ということは、マイクロフォーサーズ専用を作るとなると、それなりの理由が必要になるわけですね。
山木:そうです。
IR:しかし今の時点では、マイクロフォーサーズ用のレンズの需要はAPS-Cやフルサイズ用と比べても小さく、それほど多くはありません。
山木:その理由の一つは、マイクロフォーサーズにはもう既にたくさんの種類のレンズがあるからでしょうね。
IR:ああ、確かにそうですね。
山木:マイクロフォーサーズのユーザーは現在のレンズラインナップに十分満足していると感じます。それに対して、ソニーのEマウントはあまり多くのレンズはありませんから、私たちもたくさん要望を受けますね。
IR:Eマウントはフルサイズも出ているので、需要が大きいのはそのせいかもしれません。シグマにはとても性能の高いフルサイズ用のレンズもありますし。APS-C用のレンズをマイクロフォーサーズ用に流用するように、フルサイズ用のレンズもEマウントのフルサイズ用として使えそうです。
ソニーのレンズが少ないのには理由があるのかもしれません。パナソニックやオリンパスも同じような傾向があるのですが、ソニーは当初、ミラーレスカメラを初心者用として、より強く打ち出していたのではないかと思います。かつてソニーがNEXと呼んでいた当時は、ターゲットとするユーザーはコンパクトカメラからのステップアップだと捉えていたのでしょう。なので、安価なズームレンズなど、性能の良くないレンズばかり発売していました。現在では高性能なレンズのラインナップを揃えようとしていますが、まだ十分ではありません。私も個人的にソニーのミラーレスは好きなのですが、多くにユーザーにとってレンズがネックでした。
また、ソニーの高性能なレンズはとても高価なのです。つまり、一方で廉価なレンズがあり、他方で高級なレンズがあって、その間には大きな格差があります。今、山木社長は微笑んでらっしゃいますが、それはつまり「その通り!」と仰りたいからなのでしょうか?(笑)
山木:ノーコメントです(笑)
2005年発売の10-20mm F4-5.6 EX DC HSM 発売から10年になろうとしている
IR:私たちのスタッフの技術編集者から、もう一つ質問があります。古いシグマのレンズの中には最新のカメラに使うと問題が出る事があるのですが、そのようなレンズのファームウェアをアップデートしたり、チップを交換するサービスはないのでしょうか?カメラとボディそれぞれのことを考えると、単純にチップだけの問題ではないというのもわかるのですが、例えばこの編集者は10-20mm F4-5.6 EX DC HSMを使っていて、最近のニコンのカメラでライブビューによるAFが出来ないと言っています。
解像度がとても高いので、70mm F2.8 DG Macroを私たちのラボでもよく使います。このレンズならボディの解像度が最高でどれくらいなのか調べることができるからです。しかし、これも同じようにいくつかのカメラではライブビューでAFが動作しません。このようなレンズのファームウェアをアップデートしたり、チップを交換する事はできないのでしょうか?
もう一つ質問があります。ライブビューに問題が出る原因は、レンズが高速に動いて止まるという動作をしなければいけないからだと思います。カメラはフォーカスを調べ、レンズが動き、また止まるという一連の動作を高速に行う必要があります。ライブビューの問題はコントラスト検出方式のAFとレンズのモーターの相性が悪いことが原因なのでしょうか?それとも、これはファームウェアで修正できる問題なのでしょうか?
山木:この件に関しては問題が2つあります。まず、そもそもこれらのレンズは静止画用に設計・開発されたということです。ライブビュー用に作られてはいないんです。ライブビューのAFというのは動画のAFととても似ていて、超音波モータはこの方式に向いていません。ステッピングモータや、ボイスコイルモータの方がライブビュー向きです。
IR:なるほど、超音波モータは高速に動いて止まるという動作が苦手なのですね。
山木:そうです。これが一つ目の理由です。もう一つの理由はファームウェアです。AFの動作をライブビュー用に最適化することは不可能ではありません。なので、今後も既存のレンズの性能を上げていくことは可能です。
シグマの超音波モータ
IR:ということは修正は可能なのですね。
山木:今後もレンズのファームウェアアップデートは行っていきます。しかし、それは既存のレンズだけです。生産停止になったレンズのアップデートは行いません。
IR:生産停止のレンズはないのですね。
山木:例えばいくつかのレンズはファームウェアのアップデートをすることでキヤノンのCinema EOS C100に対応できます。もしユーザーがUSBドックを持っていれば自宅でアップデートが出来ますし、私たちのサポートに送ってもらえればアップデートします。現在はキヤノンのCinema EOSに対応しているレンズも何本かありますし、今後もレンズのファームウェアのアップデートは行っていきます。
IR:70mm F2.8 EX DG Macroは現行モデルではないのですか?違う?もう生産停止になったのですか。残念です。これは私の一番のお気に入りのレンズなんです。ただ、もうあまり需要はなかったのでしょうね。
山木:はい、これは私の一番好きなレンズでもあります。確かに他のレンズと比べてあまり需要はありません。あと、このレンズで使ってるガラス素材がもう生産していないんですよ。
生産停止になったシグマ70mm F2.8 EX DG
IR:ああ、もうガラスメーカーから素材を仕入れることが出来ないんですか。なるほど。
山木:彼らが言うには、この素材はとても特殊なガラスなんだそうです。なので、生産を続けることはできなくなりました。
IR:それはとても興味深いですね。かつてシグマの光学設計者と話をした時に、ガラス素材の違いについて説明してくれました。特殊なガラスは通常のガラスとは全く異なる屈折をするそうですね。とても面白い話でしたが、生産停止ですか。残念です。このレンズはその特殊なガラスを使ってるからそこまで高性能なのでしょうね。
山木:そのガラスが具体的にどう影響してるのかはちょっとわからないので、技術者に聞いてみる必要がありますね。
IR:ふむ。となると、シグマが現在発売している中で非常に解像度の高いマクロはどれになるのでしょうか?70mmに近い性能のものは現行モデルだとどれになりますか?
山木:ちょっと焦点距離が長くなってしまいますけど、150mm F2.8 EX DG OS HSM APO Macroか180mm F2.8 EX DG OS HSMが匹敵しますね。とても高性能です。
IR:ああ、180mmですね。確かに高性能です。
山木:105mm F2.8 EX DG OS HSM Macroもとても良いですよ。
SIGMA 180mm F2.8 EX DG OS HSM APO Macro
IR:そうですね。でもやっぱり70mmは特別なレンズだったと思いますよ。つまり、ファームウェアに関しては現行のモデルは常にファームウェアアップデートを行い、動作の不具合に対応していくということでしょうか。今後もファームウェアは更新を続けていくと。
山木:そうです。