シグマCEO山木社長インタビュー(Fotografia 2014)(その1)
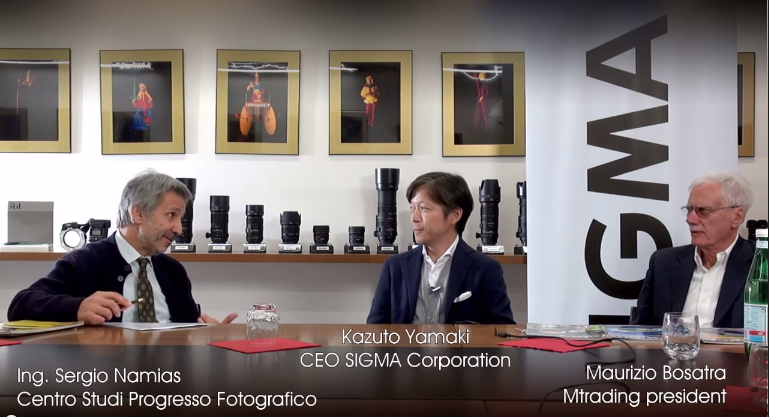
-今回はインタビューに参加いただき、大変ありがとうございます。
山木:ありがとうございます。
山木:そうです。
-それは現在も変わっていないのですか?
山木:同じです。90年代の半ばに円高が進行し、製造コストが高くなってしまいました。その結果、多くの会社が工場を中国やマレーシア、タイなどの海外に移しました。
私たちの会社でも大きな議論になりましたが、最終的に日本に残ることを決断しました。シグマは同族経営の株式非公開企業です。もちろん、売り上げや利益を向上させるのは大事なことなのですが、一番大事なのは雇用を維持することです。もし、私たちの工場を海外に移転すれば、工場で働いている従業員を解雇しなくてはいけません。海外に工場をつくりながら、国内工場も維持することは出来ませんから。
しかし、それは私の父が望んだことではありませんでした。最終的に日本に残ることに決め、そのために、製品のラインナップを変えていくことにしました。
当時の私たちの主力製品は、初心者向けのものが中心でした。高性能な製品を作るのは大変で、それだけでビジネスを続けるのは難しかったからです。しかし、製品のターゲットを初心者向けから中級、高級へと広げていくことを決断しました。
-国内で作り続けるということは製品の品質を管理しやすくなるというメリットもありますね。
山木:そうです。例えばレンズに関して言えば、製造のプロセスはどんどん複雑になってきて、これまでよりも、もっと難しくなっています。なので、経験豊富な技術者を抱えているということが、高性能な製品を作る上で、とても重要になっているのです。
このような生産方式は、実は業界でも稀です。今日では多くの企業がいわゆる「グローバル調達」方式を取っており、世界中から一番安い部品を調達して、一つの工場で組み立てています。私たちの現地での一貫生産という方法は、現代の製造業のトレンドから見ると、とても珍しいのです。しかし、私自身は、高性能な製品を作るためには、この生産方式がとても重要であると確信しています。
-私たちもシグマの製品の高い性能を確認しています。最近も誌上で50mmF1.4 Artや18-35mmF1,8 Artをテストしたのですが、とても素晴らしい性能でした。
山木:どうもありがとうございます。
-実際に私たちの行ったテストチャートを見られてはいないと思うのですが、とても感銘を受けました。シグマの製品は同カテゴリーの中で最も高性能だったのです。キヤノンやツアイスよりも数字が良くて、とても驚きました。数年前のシグマの製品とは全く違うこれらの高性能なレンズを、どうして作ることができるようになったのですか?
山木:それには三つの理由があります。まず一つ目は私たちの会社には高性能な製品を作る環境が整っているということです。昔はなかったような特性の良いガラスが今はありますので、それを使ってより性能の高いレンズを作れます。
また、コンピュータの性能も向上していますので、光線の追跡のために行う計算も、これまでより短時間で行えるようになっています。例えば私が入社した当時は、設計者がデータを入力すると計算終了まで20~30分も待ち続けたのです。現在のコンピュータはとても性能が高いので、常に光線の動きを演算をさせながら設計を行う事ができます。その結果、レンズ設計のサイクルそのものが短縮化されましたし、設計者も色々なオプションを試しながら設計ができるようになりました。
これが一つ目の理由です。しかし、これは他の会社でも同じことです。二つ目の理由は、幸運にも、私たちの会社にはとても優秀なエンジニアがいるということです。シグマでは大学を卒業したばかりの人材を雇うことが多いのですが、入社する前から、シグマは写真機材しか扱っていないということを彼らは知っています。他の製品、例えばプリンターやコピー機や半導体を作っているわけではありません。シグマはカメラしかやっていないんです。なので、写真に関わる仕事、例えばレンズの設計やカメラの開発がしたい人は、自然とシグマに入社することを希望してきます。
特にここ数年シグマに入社してきた人材は、写真やカメラに対してとても熱心です。彼らは24時間ずっとカメラやレンズについて考えています。そういう人材がシグマにはいるので、より良い製品を作ることができるのです。これが二つ目の理由です。
しかし、最も大きな理由は、繰り返しになりますが、日本の会津工場だと思います。会津工場の技術力や製造能力はとても高く、スタッフは豊富な経験を持っています。彼らは設計部から出された複雑な設計の部品でも対応できる能力があります。
これは他の会社で働くエンジニアから聞いた話なのですが、現場が設計部の注文を拒否するということが時々起こるそうです。設計がとても複雑だと、仮に製造をしたとしても、生産量はとても少なくなってしうので、効率が悪くなります。
かつて、とある会社で働いているエンジニアが「シグマのエンジニアが羨ましい」と私に話したことがあります。私たちの工場ではどんな複雑な設計でも対応できる能力や技術がありますから。
シグマの工場がそれだけの技術を持つことが出来たことをとても誇りに思っています。これが高性能な製品を製造できる理由です。
-先ほど、製造が難しいレンズという話をされましたが、例えば加工が難しいガラスというのもあるのでしょうか?FLDガラスのような特殊なレンズは取り扱いが難しいのですか?
山木:そうですね、FLDは加工が難しいガラスの一つです。FLDや、私たちがSLDと呼んでいる特殊低分散ガラスも、通常のガラスと比べて柔らかく、研磨の段階でとても慎重な取り扱いが必要です。表面に傷やヘコみがつきやすいからです。また、それと同時に、研磨をする部署では多くの人が働いていますから、そこにいる人全てが、注意深く作業をする必要があります。もし、一人の人間が注意を怠ったら、それだけでたくさんのレンズに不良品が発生してしまいます。結果的に生産量も低下します。
山木:その通りです。
-FLDガラスと蛍石との違いは何なのでしょうか?
山木:光学的な特性はほとんど同じです。ただ、製造過程が異なっていますので、FLDのコストは蛍石と比べてとても安価です。
-シグマのレンズは一つずつ、自社開発のMTF検査装置でチェックされているとのことですが、どうしてそれを始めたのでしょうか?
山木:私たちはシグマのユーザー全員にシグマの製品を楽しんでほしいと思っています。高性能なレンズを設計できたなら、その性能を全てのレンズが発揮できるようにしたいのです。そのために、すべてのレンズを検査する必要がありました。
-しかし、実際にすべてのレンズをチェックするのは大変なのではないですか?他の会社は全数検査を行っていないのでしょうか?
山木:他の会社がどのような検査体制なのかは詳しくはないのですが、私たちにとってはあまり困難な作業というわけではありません。単純に組立ラインの最後に検査があるだけなので、製造時間が少し多めにかかるということだけです。
それよりも難しかったのは検査装置を自分たちで開発するということでした。そして、実際の検査時間を出来る限り最短にするのが最も困難でした。今使っている検査装置のA1以前にも、私たちは自社開発の検査装置を使っていました。それには通常のベイヤーセンサーを使っていたのですが、高性能なレンズを測定するための解像度が十分ではなかったのです。当時は高解像度なセンサーが業界そのものにも存在していなかったのですが、私たちは高解像度なSD1の発売間近で、ニコンもD800の発売を控えていました。
私たちには、SD1やD800に見合うだけの解像度を持つMTF検査装置が必要だったのですが、当時の検査装置はそれよりも解像度が低く、私たちも困っていました。その後、「自分たちには高解像度なSD1のフォビオンセンサーがあるじゃないか」と気づいたのです。そして、フォビオンセンサーを使った検査装置を自分たちで作ると決めました。
フォビオンを使った検査装置というのは今までになかったものなので、これを作るのはとても苦労しました。しかし、私たちはカメラを作ってきた経験がありましたので、レンズを検査するためにどうやって画像データを処理すればいいかわかっていました。実際に開発を担当したエンジニアは素晴らしい仕事をしてくれたと思います。
また、実際の組立ラインで使用するためには、検査時間は可能な限り短い必要があります。研究室や実験室で調べるわけではありませんから。エンジニアは研究を重ねて、短時間で検査ができる装置を開発してくれました。
-その検査装置を使えば短時間でレンズの様々な特性を調べることができるのですか?
山木:装置のインターフェイスそのものはとても単純で、誰でも使うことが出来ます。機械にレンズをセットしてボタンを押すだけで、自動的に検査が始まり、レンズが合格か不合格かがすぐにわかります。